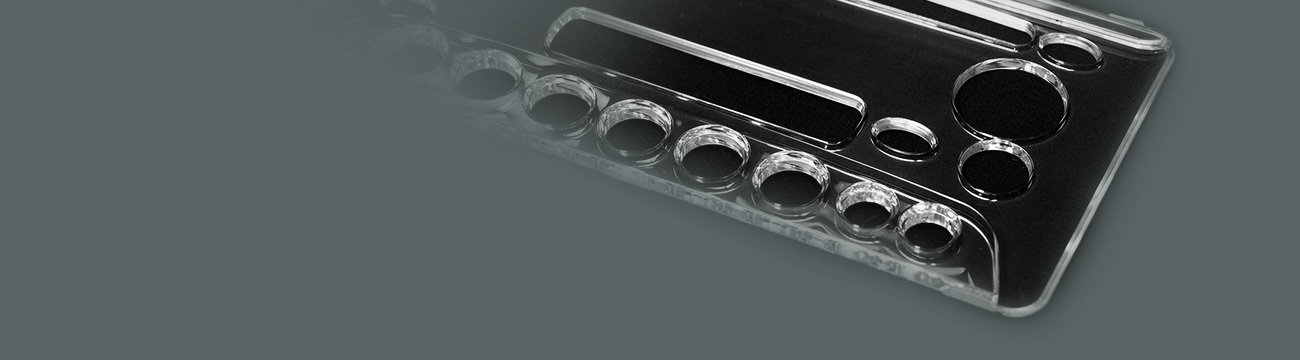
Improved glossy finish.
Superior molded parts without weld lines
offering better
aesthetics and strength.
Weld lines impact the quality of the external appearance.
Our own technology that prevents weld lines produces superior products.
Improving the glossy finish eliminates the need for a coating process,
and it also has excellent strength.